MOLD MAKING
From initial concept to mold manufacturing, our shop handles the mold making process from start to finish:
- Design: Our engineers will create a custom mold design from your initial concept.
- Approval: You’ll review and approve 2D and 3D models (CAD/CAM) of your design before production begins.
- Production: Under the careful supervision of our production managers, your mold design heads to our shop floor for manufacturing.
- Delivery: Upon completion, we’ll deliver your mold from our Massachusetts facility and test it to be sure it’s working correctly.
Our project management team sends status updates and coordinates with you every step of the way.
Our full Customer Order Process:

Plastic Injection Molds
Injection molds are the heart of modern manufacturing. When you’re producing on a mass scale, precision and quality are imperative. That’s why every one of our molds undergoes rigorous testing and inspection during the mold making process.
F&M produces injection molds for many different industries. We’ve manufactured models for:
- Safety gear
- Surgical devices
- Medical implants and wearable devices
- Cutlery (forks, knives, spoons, handles)
- Automotive body parts, fuel components, and dash panels
- Home appliance covers
- Housewares (dish racks, cutting boards, etc.)
- Defense and military projects (ITAR Registered company)
- …and more
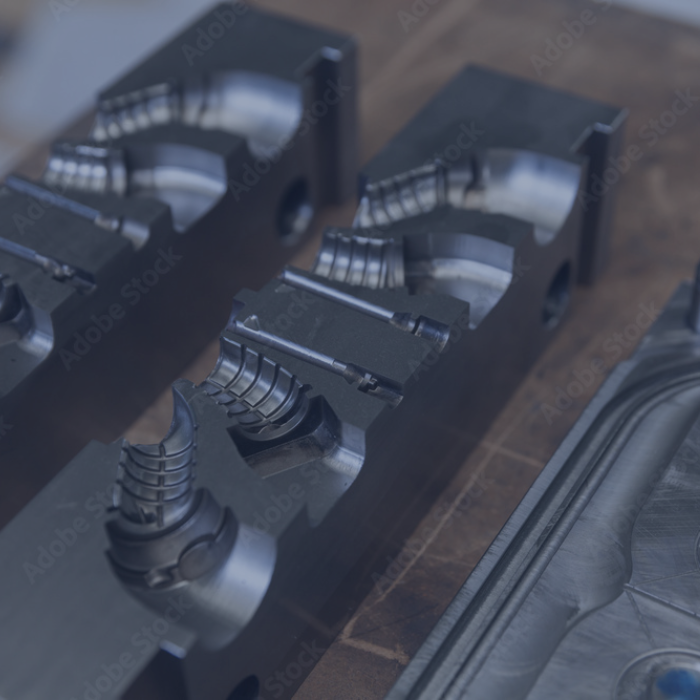
Die-Cast Dies
Our metal tool-making process combines traditional trade practices with cutting-edge computer technology. Components made with die-cast dies are durable, heat-resistant, and replicable with the highest degree of accuracy.
F&M can produce all types of dies: single cavity, multiple cavity, combination, and unit. We’ve created die-cast tools for:
- Medical devices
- Surgical tools
- Automotive body parts
- Industrial equipment
- Lighting components
- Hardware
- Defense and military projects (ITAR Registered company)
- …and others
How are Molds for Plastic Injection Made?
- Designing the Mold:
- Product Design: The first step is to have a design for the plastic part that needs to be produced. This can be created using computer-aided design (CAD) software.
- Mold Design: Once the product design is finalized, engineers design the mold. This includes creating the mold cavity, core, and other necessary features.
- Material Selection:
- Mold Material: The material for the mold is chosen based on factors such as the type of plastic to be used, the expected production volume, and the desired mold life. Common materials for molds include tool steel and aluminum.
- Machining the Mold:
- CNC Machining: Computer numerical control (CNC) machines are used to cut and shape the mold components with high precision. This step involves milling, drilling, and other machining processes.
- EDM (Electrical Discharge Machining): In some cases, EDM is used to create complex shapes that may be difficult to achieve with traditional machining.
- Heat Treatment:
- Hardening: Depending on the material used, the mold may undergo heat treatment processes such as hardening to enhance its durability and resistance to wear.
- Assembly:
- Fitting Components: The different components of the mold, such as the cavity and core, are assembled and fitted together. Cooling channels may also be incorporated to regulate the temperature during the injection molding process.
- Surface Finish:
- Polishing: The mold surfaces that come in contact with the plastic are polished to achieve a smooth finish. This helps in producing high-quality plastic parts with a good surface finish.
- Testing and Adjustments:
- Trial Molding: Before mass production, a small number of test runs are performed to check the mold’s functionality and identify any issues.
- Adjustments: If necessary, adjustments are made to optimize the mold for consistent and accurate production.
- Final Inspection:
- Quality Check: The completed mold undergoes a thorough inspection to ensure all dimensions are accurate, and the mold meets the required specifications.
- Production:
- Once the mold passes inspection, it is ready for mass production. The mold is installed in an injection molding machine, and plastic is injected into the cavity to produce the desired parts.
The entire process requires precision engineering and attention to detail to ensure the mold can produce high-quality plastic parts consistently over its lifespan. The complexity of the mold-making process can vary based on factors such as the part’s design, material requirements, and production volume.